You must be logged in to rate content!
4 minute(s) of a 620 minute read
8-17-2011
It's about time I get the shock situation figured out. As I mentioned before, I didn't like the way they were mounted to the frame before. There was a stud that came inward from the frame. In one picture I posted a while back, you can see how the bracket captured the dirt, sand and salt and created a rusting problem. Also the shock simply slid over the non threaded stud and was held in place by a cotter pin. I perfer a bolt on mount and we're gonna mount the shock brackets to the cross brace instead of directly to the frame.
First picture is just an idea of the location.
Nothing fancy here either. I'll make 4 plates like the cardboard piece here. These will mount the bottom of the shocks to the axle.
Next to be made is replacing these top plates with some new ones. These are stretched and rounded in the wrong places.
8-18-2011
I'm still short on time, yet I gotta get something done every night. I got the card board piece and scanned it in. Then went out to the shop and cut 4 shock mounting plates.
I could have had the plasma cutter cut the holes for the shock bolts. Problem is... I wasn't exactly sure where I wanted them to be. I was able to take the plate, lay it on the shock and mark the best place for the bolt hole, then drill.
Going back a few posts, a man named John asked about metal and its strengths. I mentioned the difficulty of sawing a piece of metal that had been cut with extreme heat. I also mentioned to consider your next steps of each project as to making things as easy as possible. Well here we are. I know the plasma cutter won't make as clean a cut as a drill. So if I had the plasma cutter cut the holes, I'd want to clean the hole. Now I've created a hardened surface with the plasma cutter, now I've created more work in the long run. So drilling afterwards is the better choice for me.
Ok, I want all four plates to be the same. I'm gonna drill, I need 1/2 inch holes. Personally, I stack the plates, I first drill with a 3/16 all plates at once. Now I could run a 1/2 drill through all the plates, but I'm not. Usually if I run a 1/2 inch drill now, the drilled material will get caught between the plates and start to catch on the drill bit and make a mess. For me, I remove the plates, I already have a pilot hole through each one, so just drill each one individually to the 1/2 inch size.
At this point stack'em all together and grind all the edges at the same time. It is a great idea to put a bolt through all the plates and tighten them all together, the holes are now the central immovable attachment. Sounds like a lot of hoopla for shock mounts, but if the distance from the bolt hole to the axle housing is off, you'll see the inaccuracy later when you look down from the top. I recommend also to create one plate exactly how you want them to be, then mark it with a sharpie. Always but always use this one that you compare with the others while shaping them. If you use the second plate and it's off just a bit anywhere, this inaccuracy will mulitiply itself by time you get to the fourth plate.
Comments
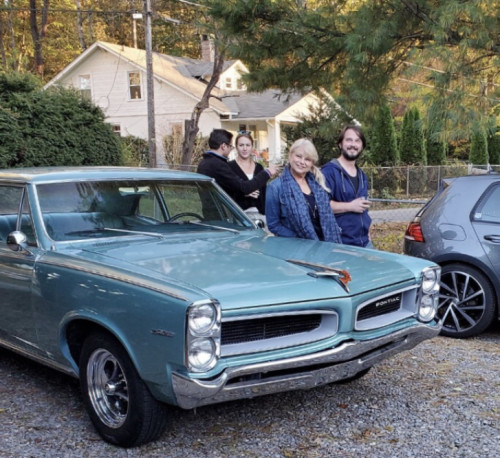
Great before & after!
Posted by Diggymart on 1/11/20 @ 4:10:28 PM
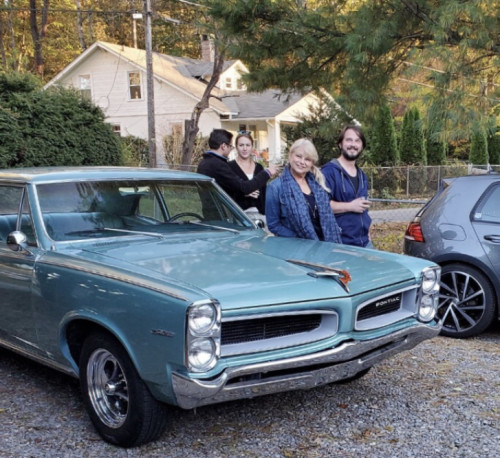
Gotta love the Willys! Good job...great build!
Posted by Diggymart on 12/10/18 @ 8:34:21 PM
Ultimate classic truck right there
Posted by CCmyVW on 12/26/20 @ 4:17:42 PM